In today’s fast-paced industrial landscape, ensuring that products are designed for efficient, cost-effective, and high-quality manufacturing is essential. This is where Design for Manufacturing (DFM) plays a crucial role. DFM is a systematic approach that focuses on designing products in a way that simplifies the manufacturing process, reduces production costs, and improves overall efficiency without compromising functionality or quality.
Monarch Innovation specializes in advanced rapid prototyping services and product development, making DFM a key aspect of ensuring smooth transitions from design to production. By integrating DFM principles early in the design phase, manufacturers can prevent costly mistakes and enhance the manufacturability of a product.
Benefits of Design for Manufacturing
Implementing Design for Manufacturing offers numerous benefits, including:
1. Cost Reduction – Optimizing designs for manufacturability reduces material waste, minimizes production errors, and lowers overall manufacturing costs.
2. Enhanced Product Quality – DFM ensures consistency in manufacturing, leading to fewer defects and improved product reliability.
3. Faster Time to Market – By addressing manufacturing constraints early in the design phase, companies can streamline production and bring products to market faster.
4. Efficient Use of Materials – DFM helps designers select cost-effective materials and optimize component designs to reduce unnecessary complexity.
5. Improved Scalability – Products designed with manufacturability in mind can be easily scaled up for mass production.
Why is Design for Manufacturing Important?
Manufacturing a product involves several stages, from prototyping to full-scale production. Without proper planning, design issues can lead to inefficiencies, defects, and increased production costs. DFM is crucial because it helps engineers and designers create products that are not only functional but also easy to manufacture.
At Monarch Innovation, we understand the significance of Design for Manufacturing in optimizing production. Our prototyping services help identify potential design flaws early, allowing businesses to refine their designs before mass production begins.
Ignoring DFM can result in:
- Increased production costs due to excessive material waste.
- Assembly and manufacturing difficulties lead to delays.
- Higher chances of product failure, increasing returns, and customer dissatisfaction.
Design for Manufacturing: 5 Key Principles
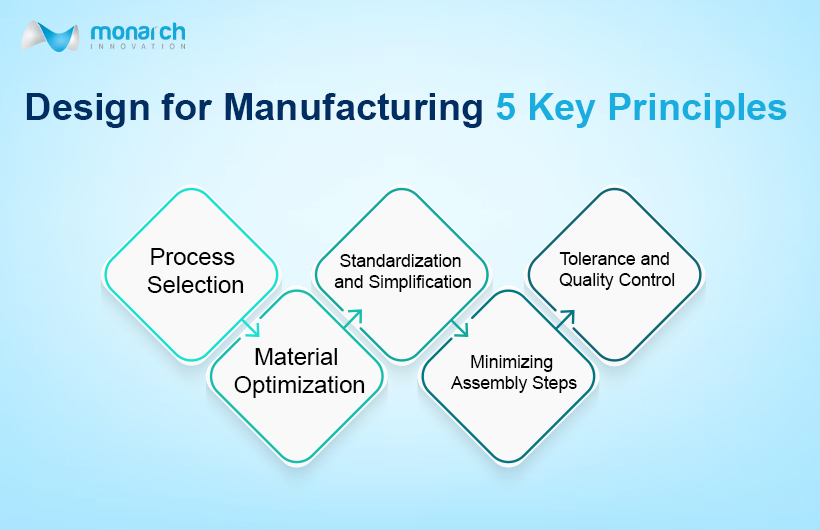
To successfully implement DFM, companies must adhere to the following five principles:
1. Process Selection
Different manufacturing processes (injection molding, CNC machining, 3D printing, etc.) have their constraints. Selecting the right process early in the design stage ensures cost-effective and efficient production.
2. Material Optimization
Choosing the right material based on the product’s function, durability, and manufacturing process can help reduce waste, improve performance, and lower costs.
3. Standardization and Simplification
Using standardized components and minimizing complex features can streamline production, reduce costs, and improve product consistency.
4. Minimizing Assembly Steps
Reducing the number of parts and assembly steps helps in decreasing labour costs and manufacturing time, improving overall efficiency.
5. Tolerance and Quality Control
Setting realistic tolerances ensures that manufacturing processes remain efficient without unnecessary precision that could increase costs.
By implementing these principles, Monarch Innovation helps clients enhance their rapid prototyping and product development processes, ensuring a smooth transition to full-scale production.
Factors that Affect Design for Manufacturing
Several factors influence the success of DFM, including:
1. Manufacturing Techniques – The feasibility of a design depends on the chosen production method, such as CNC machining, 3D printing, or injection molding.
2. Material Properties – Strength, weight, cost, and durability must align with the chosen manufacturing process.
3. Geometric Complexity – Complex designs may require special tooling or additional machining, increasing production time and costs.
4. Tooling and Equipment – The availability and cost of tooling impact production feasibility.
5. Production Volume – Low-volume production may favour rapid prototyping, while high-volume production requires optimized manufacturing strategies.
6. Environmental and Regulatory Compliance – Designs must meet industry standards and environmental regulations to ensure product safety and sustainability.
Understanding these factors helps manufacturers create designs that align with production constraints while maintaining quality and efficiency.
The Role of PLM in Design for Manufacturing
Product Lifecycle Management (PLM) plays a critical role in Design for Manufacturing by integrating data, processes, and business systems to streamline product development. PLM helps in:
- Collaboration Across Teams – Engineers, designers, and manufacturers can work together seamlessly.
- Design Optimization – Ensuring manufacturability and cost-effectiveness from the initial stages.
- Risk Management – Identifying potential manufacturing issues early to mitigate risks.
- Documentation and Compliance – Keeping track of design changes, material selections, and production guidelines to maintain consistency.
At Monarch Innovation, we leverage PLM tools to enhance rapid prototyping and manufacturing efficiency, ensuring high-quality, cost-effective product development.
Conclusion
Design for Manufacturing (DFM) is a basic strategy for improving product designs for cost-effective and efficient production. By integrating DFM principles early in the design phase, companies can reduce costs, improve product quality, and accelerate time to market.
With expertise in rapid prototyping services and advanced manufacturing solutions, Monarch Innovation helps businesses implement DFM strategies that drive innovation and success. By focusing on material selection, process improvement, and manageability, we ensure that our clients achieve manufacturing excellence.
For businesses looking to enhance their prototyping services and streamline product development, Monarch Innovation provides the expertise and technology needed to bring ideas to life efficiently and effectively.
FAQs
1. What are the 5 principles of design for manufacturing?
The five key principles are:
- Process – Select the most efficient and cost-effective manufacturing process for your design.
- Design – Simplify the design to reduce complexity, lower costs, and minimize errors.
- Materials – Choose materials early that are readily available, affordable, and easy to work with.
- Environment – Consider the manufacturing environment, such as equipment limits and production conditions.
- Testing – Design for easy testing and quality checks to catch issues early in production.
2. What are DFM and DFA?
DFM (Design for Manufacturing) focuses on making products easy and cost-effective to manufacture. DFA (Design for Assembly) emphasizes simplifying assembly processes to reduce time and cost.
3. What is DFM with an example?
DFM is optimizing a product’s design to ease manufacturing. For example, designing a plastic part with uniform wall thickness simplifies molding and reduces defects.
4. What is DfS in manufacturing?
DfS stands for Design for Sustainability. It involves designing products with minimal environmental impact, using recyclable materials, and energy-efficient processes.
5. What are the DFM rules for PCB?
Key DFM rules for PCBs include proper trace width, spacing, pad sizing, avoiding acute angles, and ensuring clearances for manufacturing tolerances.