As the demand for efficient and cost-effective 3D printing solutions grows, the debate between SLM vs SLS continues to shape the future of additive manufacturing. The industrial sector mostly prefers SLS 3D printing (Selective Laser Sintering) above SLM 3D printing (Selective Laser Melting) because of the particular technological advantages that SLS provides.
Advantages of SLS over SLM
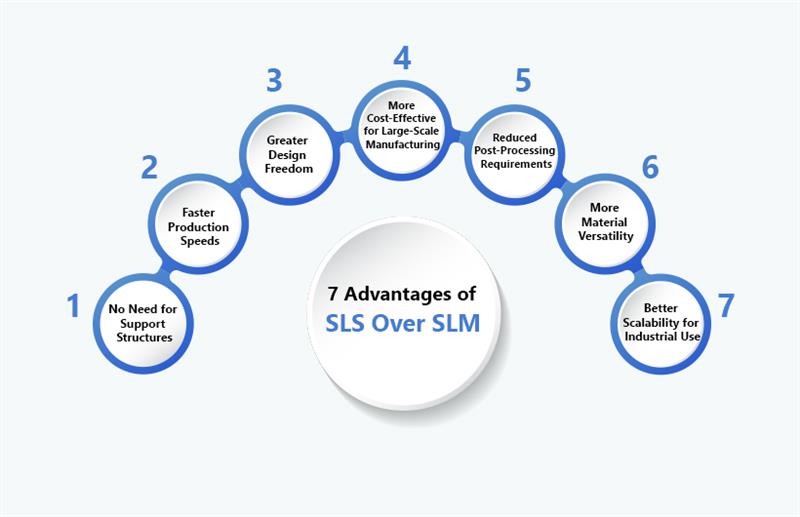
The technology improvements of SLS in 2025 will strengthen its attractive features beyond SLM, making it more applicable for aerospace industries alongside automotive and healthcare applications. The manufacturing benefits that SLS 3D printing provides surpass those of SLM 3D printing through the following seven factors.
1. No Need for Support Structures
The main advantage of selecting SLS 3D printing instead of SLM 3D printing is that support structures become unnecessary to proceed. Part production during SLM 3D printing requires supplemental support systems that generate excess materials along with additional post-printing work. The natural support system in SLS which uses unfused powder helps decrease material expenses and operating costs.
2. Faster Production Speeds
The procedure of SLM 3D printing requires longer durations to melt individual metal powder layers because it operates through a complex process. The composition of polymer and composite powders occurs at rapid speeds when using SLS 3D printing technology with its high-power laser. The SLS manufacturing method achieves high-speed operations that produce quick product creation together with wide-scale production making it the preferred manufacturing solution for prototypes and mass commercial demands.
3. Greater Design Freedom
Among SLM vs SLS methods, SLS provides designers with better flexibility during their work. Selective Laser Melting 3D printing depends on support structures as a necessity which restricts the possible geometries that the printer can create. The lack of support requirements in SLS 3D printing enables producers to create lightweight high-performance parts with intricate designs.
4. More Cost-Effective for Large-Scale Manufacturing
The high expense of SLM 3D printing stems from its metal powder materials and supplementary manufacturing processes despite its strong ability to create dense metal elements. The production of bigger batches in SLS 3D printing becomes more economical because nylon composites and polymers along with plastic materials have cheaper base costs and better availability levels. Large manufacturers seeking efficient and cost-effective scaling activities most commonly select SLS 3D printing systems over SLM 3D printing systems.
5. Reduced Post-Processing Requirements
The printed parts from Selective Laser Melting 3D printing require multiple post-processing steps for support removal heat treatment and finish surface preparation. The post-printing workflow is shortened by SLS because the technology creates parts with smooth surfaces directly from the device without needing additional support structures. The application of SLS by manufacturers enables them to minimize both time consumption and production expenses during post-production activities.
6. More Material Versatility
The material versatility assessment plays an essential role during the SLM vs SLS comparison. SLM 3D printing technology works exclusively with metal powders but SLS 3D printing allows manufacturers to process various materials such as nylon in addition to glass-filled composites and flexible polymers. SLS delivers superior performance in applications that need flexible components and items that must resist impacts while remaining lightweight.
7. Better Scalability for Industrial Use
The rapid advancement of automation and high-speed processing makes SLS 3D printing more suitable for wide industrial applications. Selective Laser Melting 3D printing operates for generating high-performance metal parts, but its focus lies in small quantities, while SLS 3D printing excels at large-scale production across various industries. The system’s scalability gets a boost from the possibility of creating multiple components with each production run.
Final Thoughts
Manufacturers now favor SLS 3D printing over SLM 3D printing since the former provides cost-effective solutions for both flexibility and scalability. The production strategies of industries will experience revolutionary changes through SLS components in 2025.
Businesses that want premium SLM 3D printing solutions need to find suitable SLM service providers. You should collaborate with experienced professionals to get expert guidance and SLM company recommendations if you require assistance to reach optimal 3D printing outcomes.
Partner with Monarch Innovation for Cutting-Edge 3D Printing Solutions
At Monarch Innovation, we specialize in providing top-tier SLM 3D printing and SLS 3D printing solutions tailored to your manufacturing needs. Whether you’re looking for an experienced SLM service provider or need expert advice on choosing between SLM and SLS, our team is here to help. Contact Monarch Innovation today and take your 3D printing projects to the next level!
FAQs
1. Which is better SLS or SLM?
SLS is better for cost-effective, durable plastic parts, while SLM is ideal for high-strength metal components. The best choice depends on your needs!
2. What are the disadvantages of SLS?
Disadvantages of SLS include higher equipment costs, rough surface finish, limited material options, and post-processing requirements for a smooth finish.
3. Why use SLS 3D printing?
SLS 3D printing is used for its high durability, design flexibility, and ability to create complex, support-free parts, making it ideal for prototyping and production.